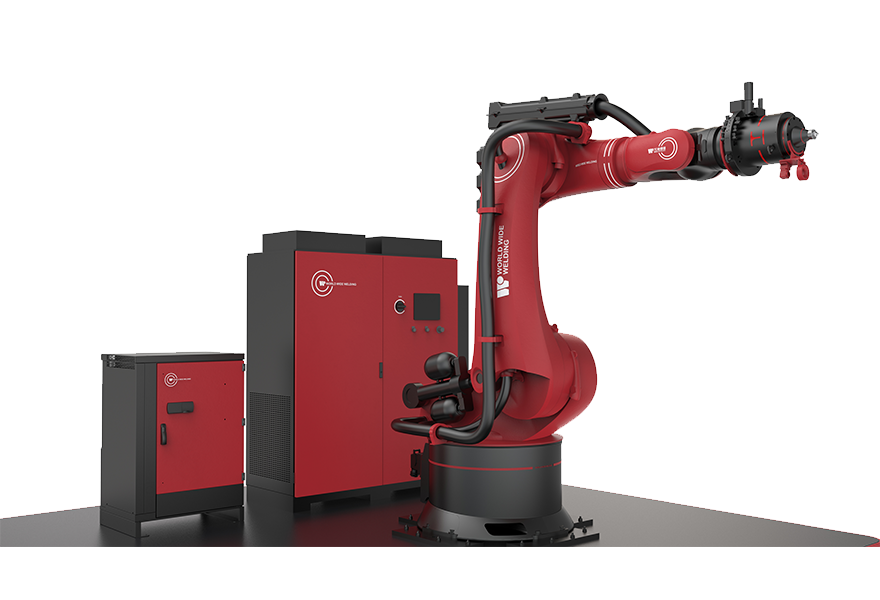
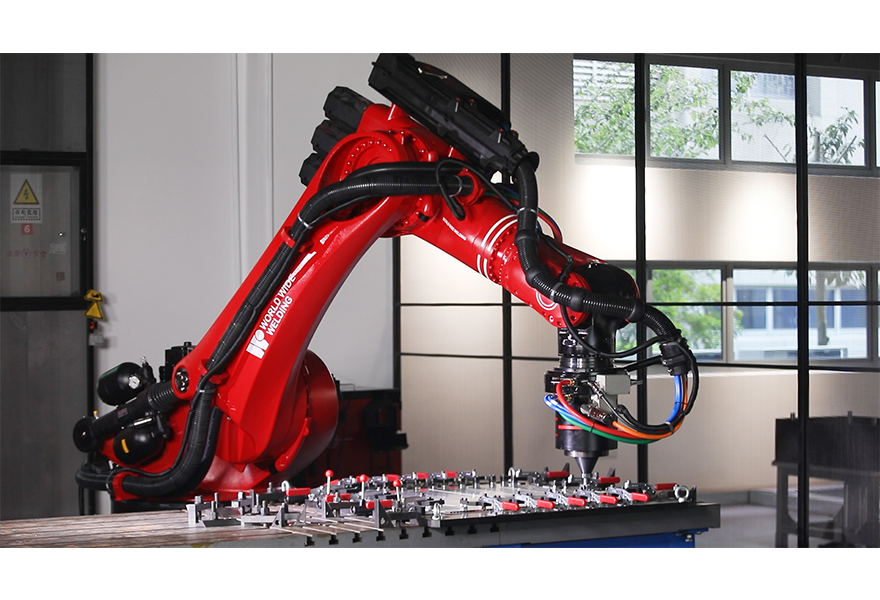
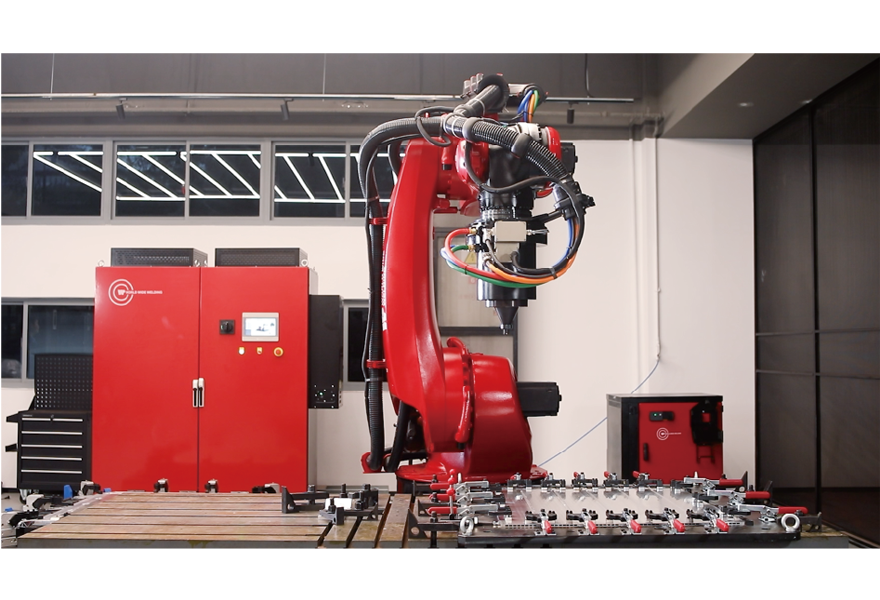
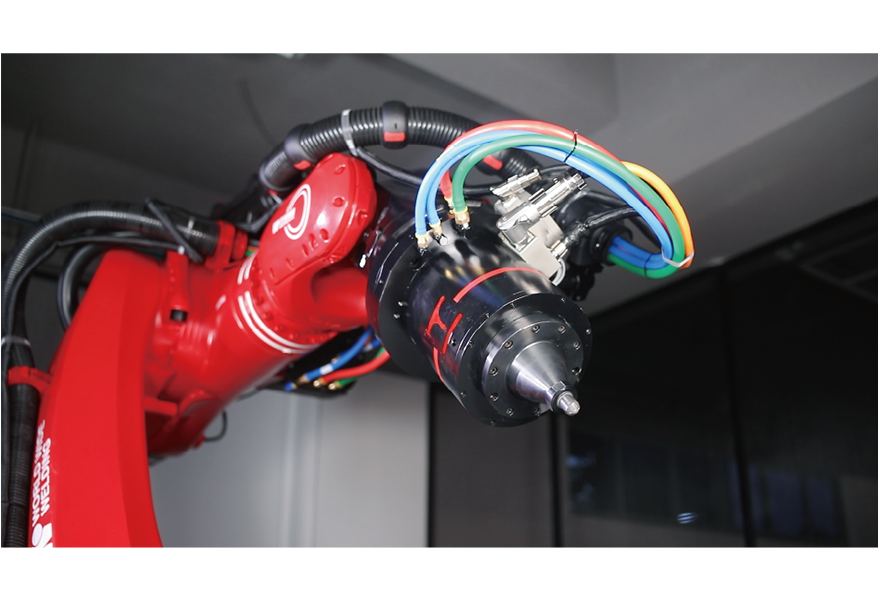
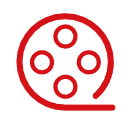
1. Product Advantages
● High flexibility
The force control system could adapt to the changes in the weld surface, which can realize the welding of the unequal thickness of the material and complex 3D welding profile.
The force-control system enables iFSW able adapt to the changes in weld face, such as the unequal thickness of the material and complex 3D welding profile.
Unequal thickness welding
Three-dimensional welding
All-position welding
● High efficiency
The maximum rotation speed of the spindle is 7000rpm; welding speed could reach 3000mm/min during mass production.
Stationary shoulder technology could realize smooth weld surface and small deformation after welding, reducing subsequent processes, including polishing shaping.
The maximum reach of the robot is 2826mm; it could realize one robotic cell with dual fixtures and one fixture with dual robots. The footprint could be as small as 24 square meters.
● Intelligent
Vision Seam Finding System: Improve the stability of welding positions to ensure the joint quality.
TPDA System (Technology Process Data Assistance System): Data monitoring, process traceability, welding tool life management, etc., can be realized by visual system during welding process.
Probe Length Detection Device: achieve automatic monitoring of welding tools to avoid defective products.
With Automatic Tool Changing Device: the automatic exchange for tools of conventional shoulder, stationary shoulder and milling tools as well as integration of welding and milling is available;
Static Shoulder Automatic Cleaning Device solves the problem of aluminum scraps accumulating on the side of the stationary shoulder to improve the lifespan of welding tools and weld quality.
Equipped with Automatic Fixture t, safety protection fences, safety light curtain systems, handling robots, AGVS. Combing with automated production lines, highly automated and intelligent unmanned welding can be achieved.
2. Product Applications
The iFSW is suitable for welding new-energy vehicle battery trays, 5G heatsink tanks, Vacuum chambers, rocket fuel storage tanks, and 3D curved controller housing.
New-energy vehicle battery tray assembly
New-energy vehicle battery tray plate
New-energy vehicle controller housing
5G heatsink tank
Vacuum chamber
Rocket fuel tank
3. Client Cases
WWW is an international leader in iFSW technology and has participated in mass production projects, including DAIMLER, BMW, VOLVO, BYD, PSA, GAC, BAIC, and other well-known automobile enterprises, providing customers with automated FSW solutions and technical services for the whole project cycle.
PSA project (One robotic cell with three-fixtures)
DAIMLER Project (One robotic cell with three-fixtures)
3 series aluminum /6 series aluminum penetration lap welding
5 series aluminum/die cast aluminum penetration lap welding
4. Basic Parameter
Model | H1K500 |
Robot | KR500 R2830 MT |
Spindle | Independent R&D |
Rated rotation speed/rpm | 4000 |
Maximum rotation speed/rpm | 7000 |
Spindle rated output torque/N·m | 76 |
Spindle power KW/kw | 32 |
Maximum welding speed mm/min | 3000 |
Maximum welding depth(6xxx aluminum alloy)/mm | 8 |
Maximum force/N | 8000 |
Robot Maximum Reach/mm | 2826 |
Pose Repeatability/mm | ±0.08 |
Welding process | Conventional shoulder FSW & stationary shoulder FSW |
Spindle cooling mode | Circulating water cooling |
Welding tool cooling mode | Center air cooling |
Holder clamping mode | Hydraulic |
Process control mode | Force Control |
Tooling layout design | One-robot with multi-fixtures/Multi-robot with one-fixture |
Optional system | Laser Seam Tracking System, Vision Seam Finding System, TPDA System, Automatic Tool Changing Device, Probe Length Detection Device , Static Shoulder Automatic Cleaning Device |