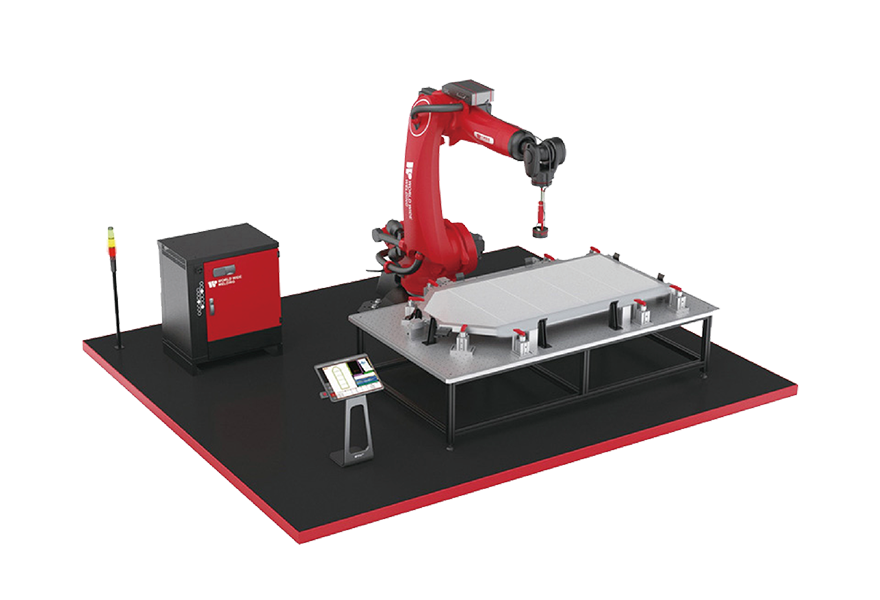
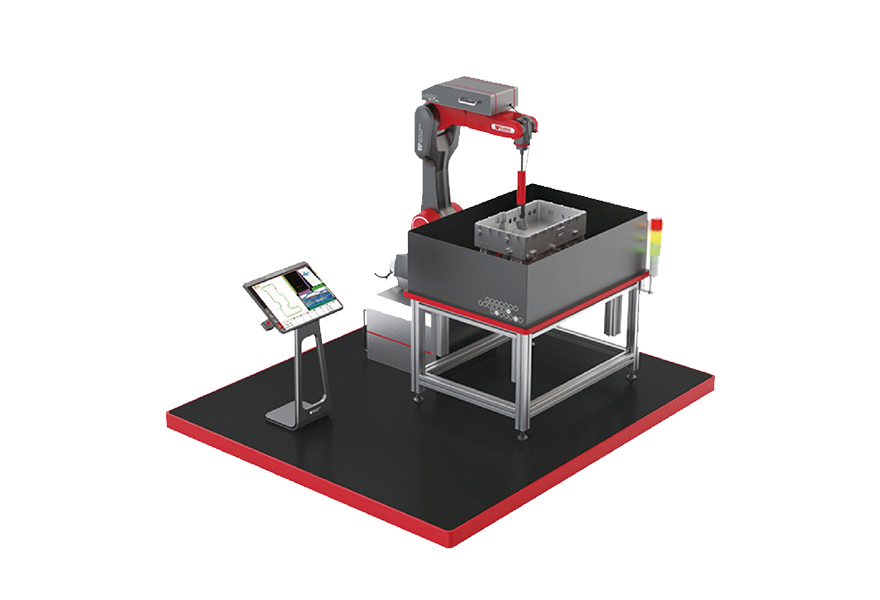
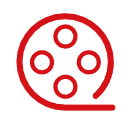
1. Product Applications
The machine applies to the non-destructive testing of welds for products including electric vehicles battery trays, motor housing, controller housing, HFCV electric reactor housing, various water-cooled radiator, rail carriage floor/wall panels, and 5G heatsink tank.
![]() | ![]() |
New-energy vehicle battery tray | New-energy vehicle motor housing |
![]() | ![]() |
New-energy vehicle controller housing | Brazed cooling plate |
![]() | ![]() |
HFCV electric reactor housing | Rail carriage floor and wall panels |
2. Technical Features
![]() | ![]() |
Defective | Detection display |
![]() | ![]() |
Non-defective | Detection display |
● Coupling mode: water-jet coupling and water-immersion coupling
● Defect identification mode: automatic identification
● Recognition mode: feature comparison/deep learning
● Contact condition: contact/non-contact
● Workstation layout: single-machine with multi-fixtures / multi-machines with single- fixture
3. Product Advantages
Automatic identification and detection
Non-contact detection
● Group standard setter
WWW organized and developed a group standard of T/CWAN 0033-2021 Phased Array Ultrasonic Detection Specification for Aluminum Alloy FSW Volumetric Defect.
Further, we were involved in developing the group standard of T/CWAN 0027-2022 Welding Manufacturing Specification for New-energy Vehicle Aluminum Alloy Battery Tray.
● Complex structure welds can be detected
The wedge can avoid contact with the workpiece and achieve non-contact detection through immersion in water to reduce the wear.
Welds that occur in surrounding complex structures can be detected.
● Automatic identification
The phased array ultrasonic testing machine can be used to avoid missing detection occurring in traditional ultrasonic detection. Moreover, Multi-angle scanning can be achieved by a phased array ultrasonic probe.
The machine can automatically identify defects to eliminate interference of human factors and avoid missing defects.
● Test process data tracing
It can automatically output detection reports and timely save the detection process data to facilitate the later detection process traceability.
● Flexible hardware collocation
It can be integrated with a robot to detect complex workpieces.
It can also be integrated with a gantry machine or automatic detection vehicle to realize long-straight weld detection.
● Automated workstation
It can complement automatic welding equipment to realize the integration of welding and testing, thus ensuring the rate of qualified products.
4. Customer Cases
WWW is the first company that can provide intelligent phased array ultrasonic automatic testing systems and testing services for FSW welds. Each machine detects 30-50 sets per hour, and we have been successively providing inspection services for BMW, Mercedes-Benz, BYD, Huawei, SAIC, and many other new energy vehicle brands.
Model: S1K2700
Project name: Welds testing for an energy storage box
Project Time: 2022.04
Tested product: Energy storage box
Welding process: FSW
Detection mode: Full testing
Detection speed:1800mm/min
Model: S2K1100
Project name: Weld seam inspection for a new-energy vehicle controller housing
Project Time: 2022.05
Tested products: Controller housing
Welding process: FSW
Detection mode: Full testing
Detection speed:1500mm/min
5. Basic Parameters
Model | S1K2700 | S2K1100 |
Maximum recognition frequency/Hz | 30 | 30 |
Minimum defect identification size/mm | 0.2 | 0.2 |
Ultrasonic digital frequency/MHz | 100 | 100 |
Maximum pulse rate/KHz | 25 | 25 |
Probe Frequency/MHz | 10 | 10 |
Number of wafers/pcs | 64 | 64 |
Maximum Testing speed mm/min | 3000 | 3000 |
Maximum detection depth (for aluminum alloy)/mm | 20 | 20 |
Maximum action radius /mm | 2696 | 1101 |
Repeat positioning accuracy/mm | ±0.06 | ±0.03 |