Technical Principle
Friction Stir Welding (FSW) is a solid-phase joining technology. The high-speed rotating tool plunges into the workpiece and moves along the welding direction, and the contact area between the tool and the workpiece generates heat through friction. As a result, metals are plastic softening. The softened metals fill the cavity formed behind the tool. The metal realizes solid-phase bonding under the function of stirring and forging force.
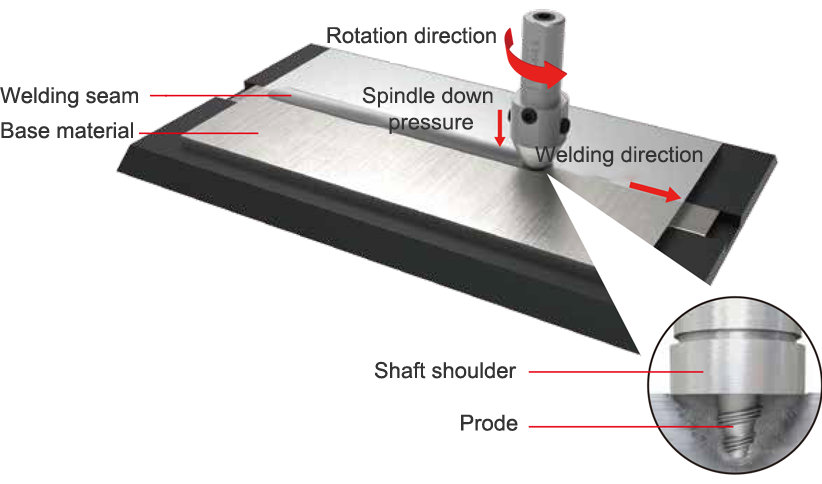

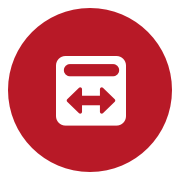
High adaptability
It can adapt to a wide range of environments unaffected by ambient temperature and humidity.
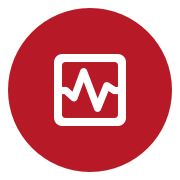
Good property
The weld nugget area forms a dense "forged structure" (equiaxed grain).
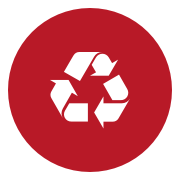
Eco-friendly&safe
The welding process does not generate arc light, smoke, or spatter. It is safe, green, and eco-friendly.

Less deformation
No material melted, Less heat input, thus less deformation.
Major Process
WWW is market-oriented and has a world-class R&D team. Through an efficient scientific research transformation mechanism, it has the world's leading friction stir welding technology.
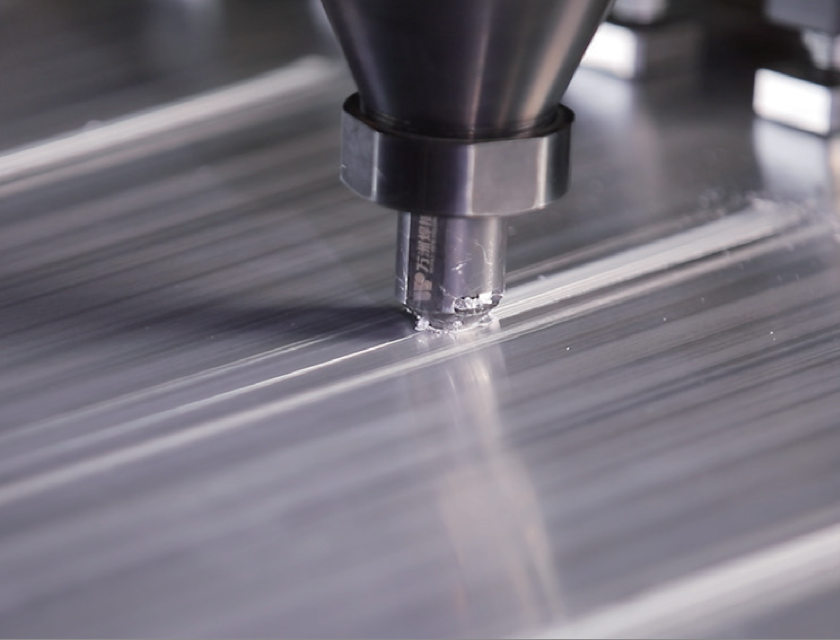
Stationary shoulder Friction stir welding
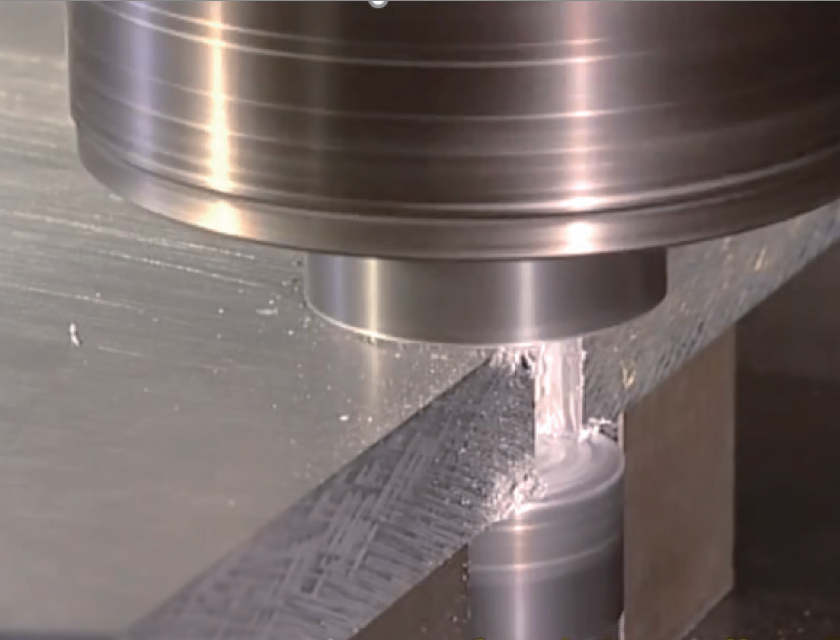
Bobbin tool friction stir welding
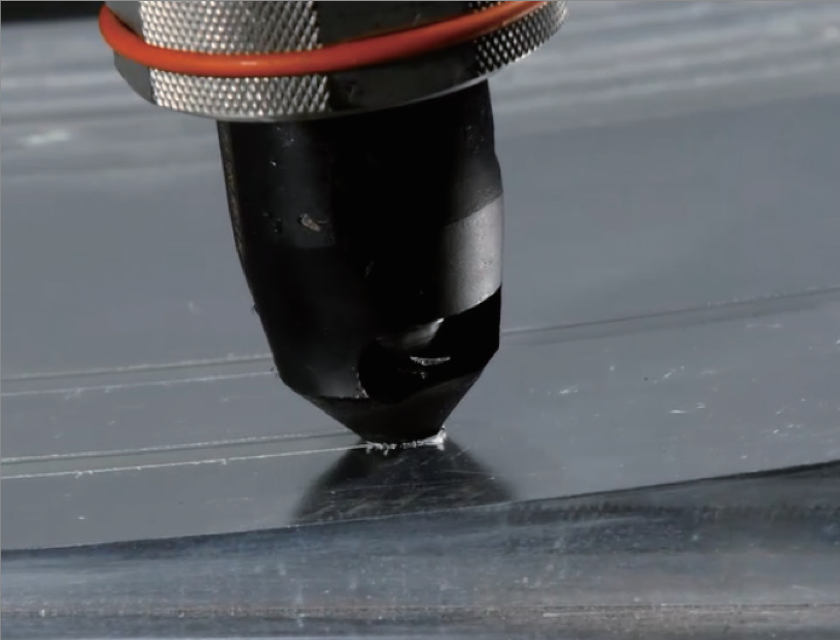
3D profile Friction Stir Welding
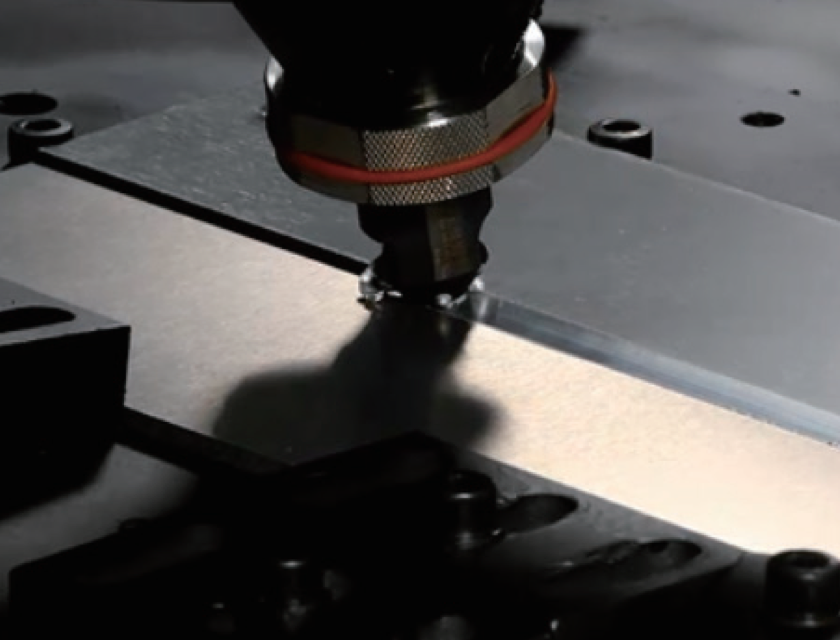
Unequal thickness welding
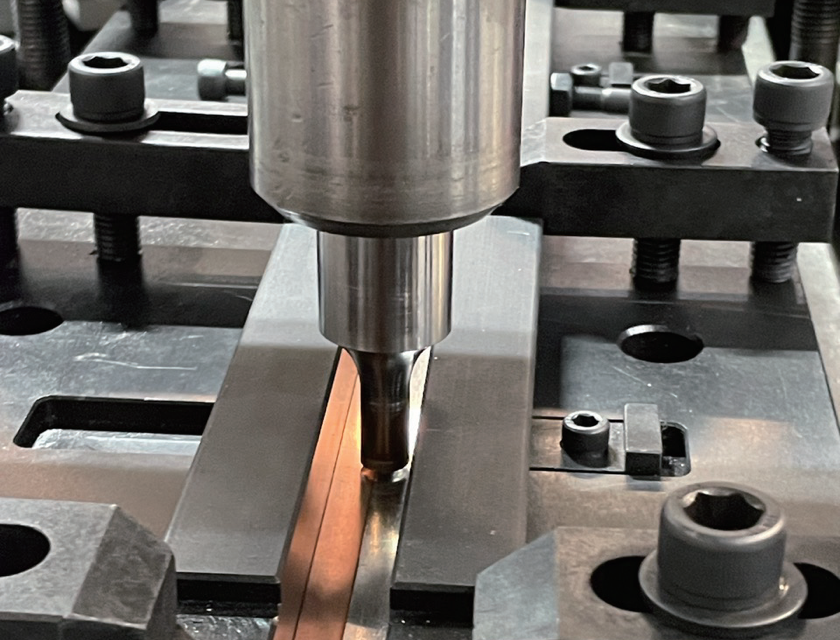
Friction stir welding of dissimilar material
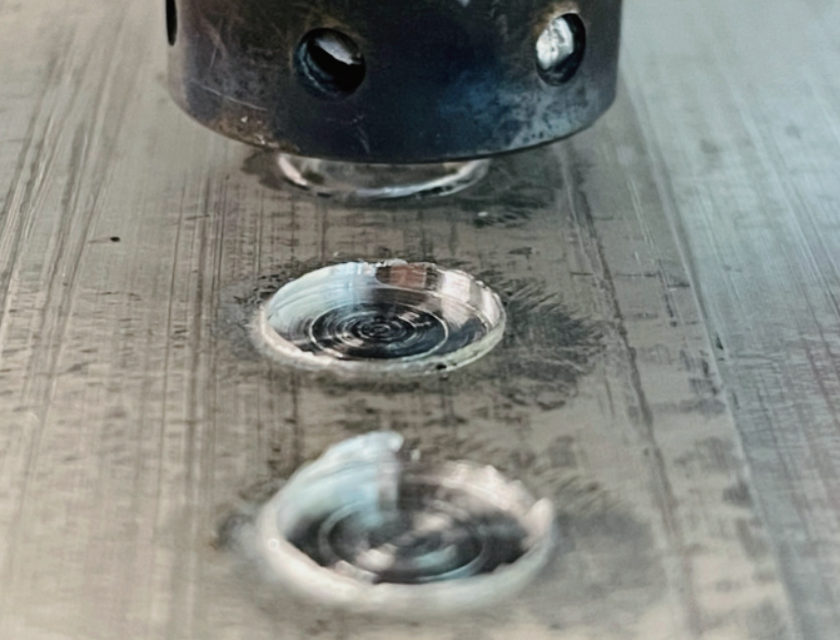
Refill Friction Stir Spot Welding
Leading Technology
WWW has an R&D team of over 60 full-time R&D staff, including three national high-level talent experts and seven welding doctors.
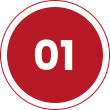
We developed filler and self-supporting friction stir welding technology.
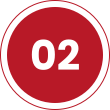
We successfully realized the industrialization of extensive-size aluminum copper dissimilar metal FSW technology.
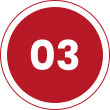
We have successfully developed the Robotic Friction Stir Welding Machine in China to achieve high-speed welding of 3D curved surfaces.
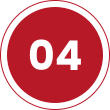
We have successfully developed leading-edge weld seam non-destructive inspection technology for volume manufacturing
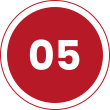
We successfully developed the first Friction Stir Additive Manufacturing Machine in China.
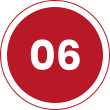
We successfully developed the Robotic Refill Friction Stir Spot Welding Machine and took the lead in realizing industrial applications in China.
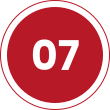
We independently developed the Friction Stir Welding and Milling Center to realize the integration of welding and machining.
Technical Consulting
WWW provides customers with technical support and customized solutions such as solution evaluation, technology development, product trial production, and product testing. We accumulated evaluation and development of various products 50000+, a total of 2000+ product proofing trial production, and 200+ welding automation solutions.
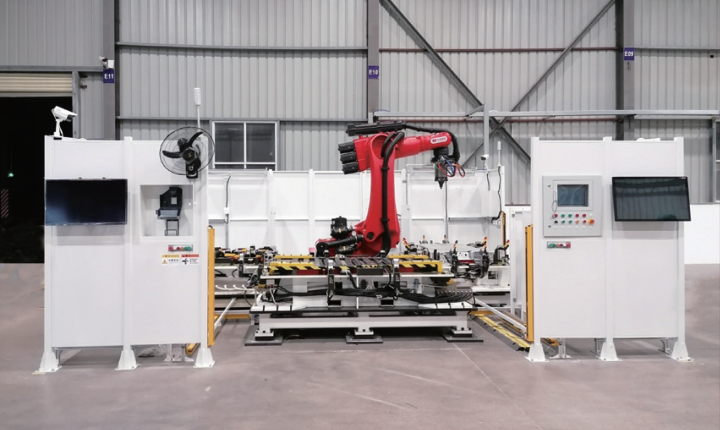
PSA project (One robotic cell with three-fixtures)
Project Name: PSA project (One robotic cell with three-fixtures)
Technical Advantage: A single machine with three stations is more flexible to help customers improve production efficiency (three different products can be produced together).
Technical Advantage: A single machine with three stations is more flexible to help customers improve production efficiency (three different products can be produced together).
DAIMLER Project (One robotic cell with three-fixtures)
Project Name: DAIMLER Project (One robotic cell with three-fixtures)
Technical advantage: This project is the first fully automated production line, which has passed the PPAP of OEM in 2021 and is now in mass production.
Difficulties: The pallet size is 2m*1.5m with 20 welding seams, and the deformation after welding is controlled within 1.5mm.
Technical advantage: This project is the first fully automated production line, which has passed the PPAP of OEM in 2021 and is now in mass production.
Difficulties: The pallet size is 2m*1.5m with 20 welding seams, and the deformation after welding is controlled within 1.5mm.
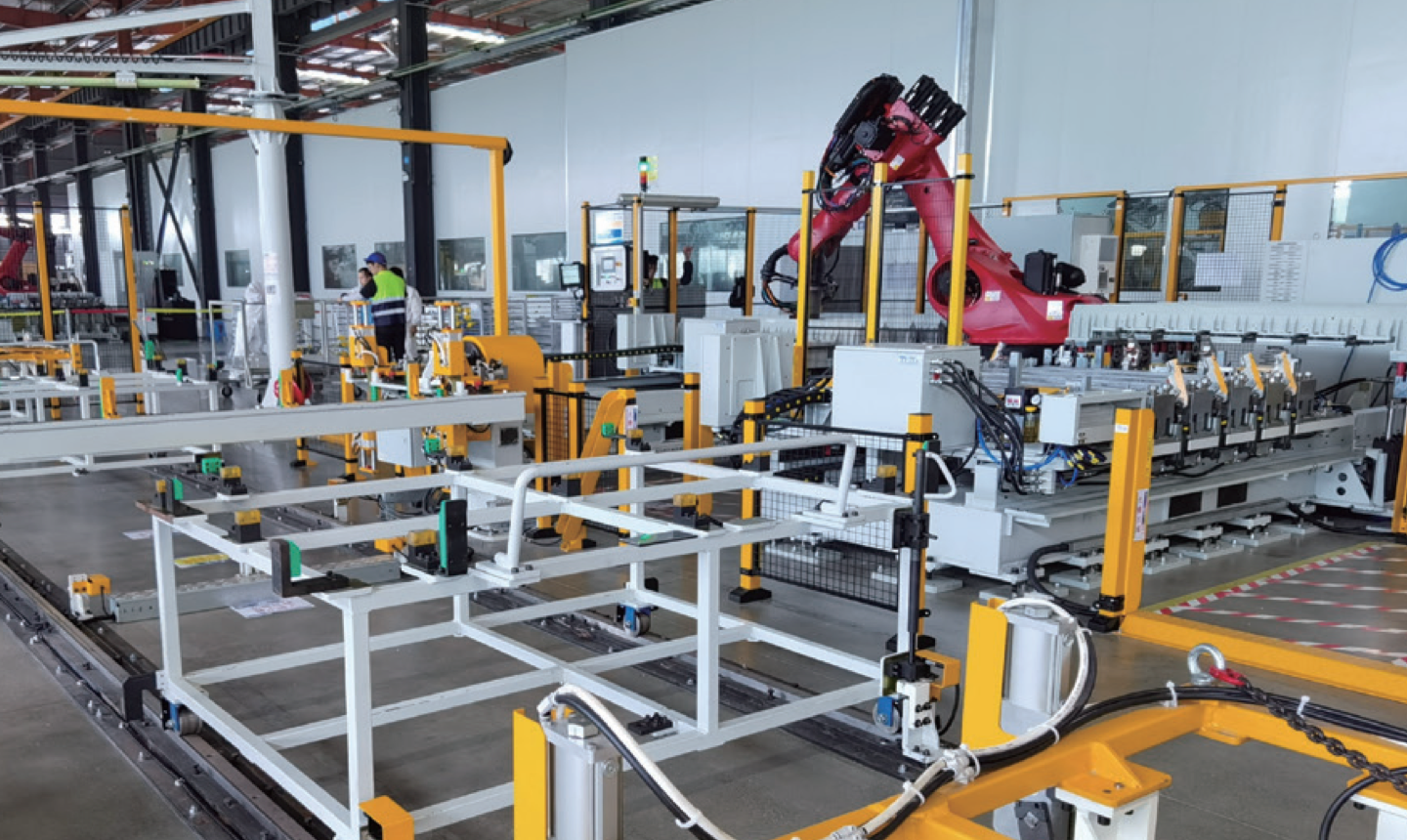
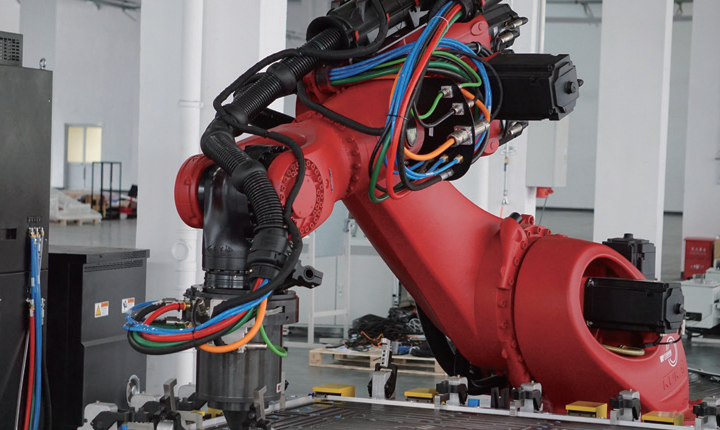
3 series aluminum /6 series aluminum penetration lap welding
Project name: CATL project (single machine with two stations)
Technical Advantage: This project uses the robot static axis shoulder process to overcome the problem of a 3-series brazing thin plate that is easy to bulge and roll up the edges, unsuitable for welding, and realizes batch welding of 1800mm/min.
Technical Advantage: This project uses the robot static axis shoulder process to overcome the problem of a 3-series brazing thin plate that is easy to bulge and roll up the edges, unsuitable for welding, and realizes batch welding of 1800mm/min.
5 series aluminum/die cast aluminum penetration lap welding
Project name: Honda one-piece die-casting project
Technical advantages: Realize the FSW of 5-series stamping plate and die-casting box, which has now passed the verification of OEMs; the first international equipment supplier of one-piece die-casting with full FSW, and successfully overcome the welding problem of 5-series stamping plate and one-piece die-casting (the length of the weld seam is close to 30m).
Technical advantages: Realize the FSW of 5-series stamping plate and die-casting box, which has now passed the verification of OEMs; the first international equipment supplier of one-piece die-casting with full FSW, and successfully overcome the welding problem of 5-series stamping plate and one-piece die-casting (the length of the weld seam is close to 30m).
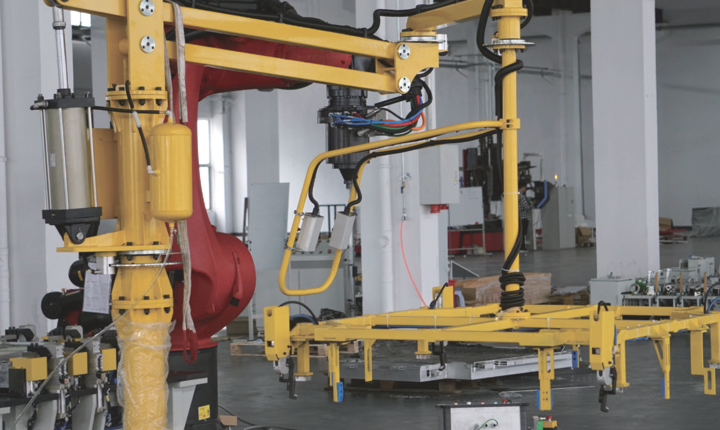
WWW has always been innovation-driven, focusing on technological innovation and intellectual property protection. We have carried out a series of technology development and patent application work around new processes and equipment, such as stationary shoulder welding and the iFSW. More than 200 patents have been applied for, including 83 invention patents and 146 authorized valid patents.